Wooden structural materials, combining high strength, environmental friendliness and ease of installation, are widely used in modern low-rise construction for the construction of roofs, ceilings and the power frame of the floor. A correctly calculated distance between the floor lags and interfloor beams is the key to the strength and durability of not only a single structural element, but the entire structure as a whole.
What are floor joists?
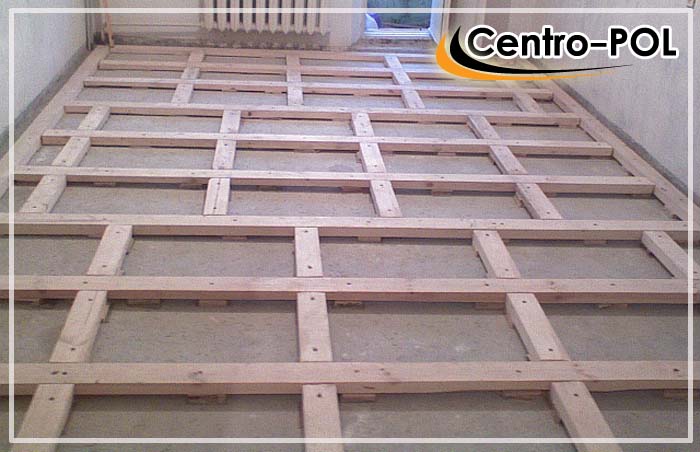
Floor logs, made of a wooden beam of a certain, precisely calculated section, are power elements that perceive static loads from furniture, equipment installed on the floor, and dynamic loads that occur when people move indoors. Floors on wooden logs have some features that allow leveling minor flaws in building structures:
- Uniform distribution of the load on the underlying building structures;
- Increase the overall strength of the floor or ceiling;
- Improvement of soundproofing properties with the formation of an additional heat-insulating layer;
- The possibility of laying engineering communications with a relatively high maintainability;
- Low complexity of installation, providing a flat surface for flooring from sheet or roll materials and flooring from natural wood of valuable species.
Logs are made mainly from coniferous wood, the resin content of which provides protection from moisture and a long service life. For the installation of logs in difficult-to-use premises, hardwoods with high moisture resistance or larch products with a high content of natural resins are used.
Why is it necessary to calculate the distance between the lags?

Like any other structural materials, wooden products have certain indicators of strength, wear resistance, service life and, of course, prices. When installing wooden floors on logs or interfloor beam ceilings, you can also use thick logs laid at a close distance from each other, obtaining the highest structural strength and spending a fairly significant amount. But the use of the required number of logs or beams, having a section corresponding to the intended load, will make it possible to obtain the necessary structural strength at a much lower cost.
In a panel house, when the logs are laid on the surface of a reinforced concrete floor slab, their cross section is selected to be the minimum necessary for attaching a floorboard or chipboard. Another thing is the use of wooden structures in a frame structure, when the logs serve not only as the basis for the future floor, but also serve as a strength element of the frame associated with wall supports.
Main calculation criteria
- The thickness of the floorboard or board materials OSB, chipboard;
- The number of support points or the distance between the walls;
Even with such minimal data, it is possible to correctly calculate the required cross-section of a wooden beam for the manufacture of logs and the maximum step between logs.
Bar section

The cross section of a wooden beam for the lag device is selected depending on the distance between the supports and the required load capacity of the floor. When calculating the required section of the lag, you should take the maximum load on the floor no more than 300 kg per m 2.
As a log, a beam of square or rectangular section is used, the wider side of which is located vertically. Thus, the maximum rigidity of the log is obtained with a minimum consumption of wood, which reduces unproductive costs for flooring. In construction practice, the ratio of the width of the log to its height is 1.5-2, which is optimal in terms of strength and cost. When using a standard edged board with a thickness of 5 cm as a log, its height with a gap between supports of 2 m should be from 10 to 15 cm. The standard dimensions of the log, depending on the span, are presented in the table:
Sometimes it is difficult for an individual developer to find a standard timber suitable for the manufacture of logs of the required section. The way out of this situation is quite simple. To ensure the required load capacity of the floor, several standard boards 5-6 cm thick can be installed side by side, increasing the height of the resulting timber by 1-2 cm relative to the standard one. Such a “layer cake”, even in the absence of fastening the boards to each other, completely replaces a full-bodied timber of the required size. Similar results can be achieved if the boards are placed at regular intervals along the entire length of the foundation bearing surface.
The only thing to consider is that in a frame house it is rather difficult to apply this method of load distribution due to the lag being tied to the racks of wall structures, openings and the distribution of insulation. In a frame house, floor logs are used as floor beams, so the minimum required cross section should be increased taking into account the load from ceiling structures and insulation.
Step between lags
In the manufacture of wooden floors, it is clearly seen how the distance between the lags, called the step from the thickness, and the type of materials used depend. The thicker the board used as flooring, the greater the distance should be between the lags. More clearly about which step to choose when using different board thicknesses, the table below shows.
As a rough floor covering in modern construction, slab structural materials are very often used instead of boards, which accordingly changes the calculation method. Chipboard (chipboard), cement-bonded particle board (CSP), oriented strand board (OSB) and gypsum fiber boards (GFP) are successfully used as a base for a coating of rolled materials or ceramic tiles arranged on wooden logs. In some cases, chipboard can be additionally coated with cement or gypsum-based materials. Considering the greater bending rigidity of chipboard and less strength than the board, you should choose a step between lags no more than 40 cm, and when using a thicker chipboard (20-22 mm), increase the step between the lags to a maximum of 60 cm.
When calculating the step between the lags for a particular room, you can use the average tabular values, and if the distance between the last lags is less, then the strength of the floor in this place will only increase.
Consequences of calculation errors

What happens if you choose the wrong section of the lag and the step between them? When installing floors on a concrete base, the most important parameter will be the step between the lags, on which the behavior of the finish coating depends. Chipboard mounted on logs installed with a greater than allowed gap may sag or break, ceramic tiles may crack, and the board may bend. In any case, the floors will require alteration.
More unpleasant consequences come from errors in calculating the required number of lags used as interfloor floors. If a larger number of logs or a larger cross section must be used than indicated in erroneous calculations, the strength of the entire structure is significantly reduced, which can lead to irreversible deformations and complete destruction of the floors.
Calculation methods
To calculate the dimensions of the beam and the number of elements required for the installation of a wooden floor on logs with rough coatings from a board or chipboard, you can:
- Contact the design organization, which will professionally calculate how many elements should be covered from a board or chipboard, and what size of timber should be used during construction;
- Use special averaged tables on your own, choosing which value is closer to the required one, leaning upwards if there is no exact match between real and tabular sizes;
- Use computer programs and online calculators, in which a sufficiently large number of parameters are entered, and the program will accurately determine the required dimensions of the beam and the distance through which it must be installed.